-
- News
- Books
Featured Books
- design007 Magazine
Latest Issues
Current IssueLevel Up Your Design Skills
This month, our contributors discuss the PCB design classes available at IPC APEX EXPO 2024. As they explain, these courses cover everything from the basics of design through avoiding over-constraining high-speed boards, and so much more!
Opportunities and Challenges
In this issue, our expert contributors discuss the many opportunities and challenges in the PCB design community, and what can be done to grow the numbers of PCB designers—and design instructors.
Embedded Design Techniques
Our expert contributors provide the knowledge this month that designers need to be aware of to make intelligent, educated decisions about embedded design. Many design and manufacturing hurdles can trip up designers who are new to this technology.
- Articles
- Columns
Search Console
- Links
- Events
||| MENU - design007 Magazine
Dave Wiens Discusses Multi-board Design Techniques
July 9, 2018 | Andy Shaughnessy, I-Connect007Estimated reading time: 2 minutes
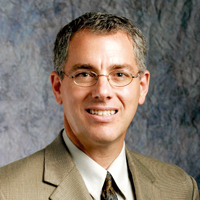
For our multi-board design issue, I interviewed Dave Wiens, product marketing manager for Mentor, a Siemens business. We discussed how the multi-board design technique differs from laying out single boards, along with the planning, simulation and analysis processes required to design multi-board systems.
Andy Shaughnessy: Dave, what are some of the typical end products that might use multiple PCBs?
Dave Wiens: The easy answer is almost every end product that includes electronics is a multi-board system. It's things down to your cell phone. If you look up your cell phone on iFixit, you'll see a tear down that's got multiple boards in there. At a minimum, there'll be, let's say a separate board for the camera or for the audio or for the external connections. Those are all separate functions and, in some cases, when somebody's designing they won't necessarily design all of those pieces. They might, for instance, be acquiring the camera from somebody else, and so that basically represents a component. It is a complete PCB, but to them it's a component because they didn't design it. We're not necessarily talking big back planes, with tons and tons of data cards on them. Certainly, that's a multi-board system, but pretty much everything you see today is multi-board.
I don't know about you, but when something in my house stops working, I tend to tear it apart. Sometimes I'm trying to figure out if I can fix it, but often I just want to see how they designed it. Really, when you're designing something and making decisions to make it into multiple boards, you start thinking about things like size and space. Should I put this all on one board? Should I break it up into multiple boards for space reasons? Should I do it because of reliability reasons? If this data board fails, it's easier to plug and play it with something else versus throwing away the whole system. Should I do it for cost reasons? Performance reasons? And then there's the make versus buy decision, right? For this particular function of my system, should I just buy a board and connect it to my system? Or should I design it into the system?
You see that with like your home PC. It's got dedicated graphics built into it now, but you still may want to put an add-on graphics card, but those used to be things that weren't necessarily integrated into one system. They've done that over time.
Shaughnessy: It sounds like some of the biggest challenges are the trade-offs you have to decide. Like, should you add another board? What are some of those challenges?
Wiens: Yes, the trade-offs are a huge one and, frankly, because of that a lot of people kind of avoid it. I mean, they make decisions very early on to segment something. They take their high-level requirements, and then they start building an architecture from that. They decide what's going to be hardware, what's going to software, and how that's going to interplay with mechanical structures, cabling structures, all of that is decided way up front, and then the question is: Do they ever revisit that? If they don't revisit it, then they were either really good and they got it right up front, or as the design progressively refines itself, as the engineers refine it from that high-level architecture down into the physical implementations, they may find things.
To read this entire interview, which appeared in the June 2018 issue of Design007 Magazine, click here.
Suggested Items
Cadence, TSMC Collaborate on Wide-Ranging Innovations to Transform System and Semiconductor Design
04/25/2024 | Cadence Design SystemsCadence Design Systems, Inc. and TSMC have extended their longstanding collaboration by announcing a broad range of innovative technology advancements to accelerate design, including developments ranging from 3D-IC and advanced process nodes to design IP and photonics.
Ansys, TSMC Enable a Multiphysics Platform for Optics and Photonics, Addressing Needs of AI, HPC Silicon Systems
04/25/2024 | PRNewswireAnsys announced a collaboration with TSMC on multiphysics software for TSMC's Compact Universal Photonic Engines (COUPE). COUPE is a cutting-edge Silicon Photonics (SiPh) integration system and Co-Packaged Optics platform that mitigates coupling loss while significantly accelerating chip-to-chip and machine-to-machine communication.
Siemens’ Breakthrough Veloce CS Transforms Emulation and Prototyping with Three Novel Products
04/24/2024 | Siemens Digital Industries SoftwareSiemens Digital Industries Software launched the Veloce™ CS hardware-assisted verification and validation system. In a first for the EDA (Electronic Design Automation) industry, Veloce CS incorporates hardware emulation, enterprise prototyping and software prototyping and is built on two highly advanced integrated circuits (ICs) – Siemens’ new, purpose-built Crystal accelerator chip for emulation and the AMD Versal™ Premium VP1902 FPGA adaptive SoC (System-on-a-chip) for enterprise and software prototyping.
Listen Up! The Intricacies of PCB Drilling Detailed in New Podcast Episode
04/25/2024 | I-Connect007In episode 5 of the podcast series, On the Line With: Designing for Reality, Nolan Johnson and Matt Stevenson continue down the manufacturing process, this time focusing on the post-lamination drilling process for PCBs. Matt and Nolan delve into the intricacies of the PCB drilling process, highlighting the importance of hole quality, drill parameters, and design optimization to ensure smooth manufacturing. The conversation covers topics such as drill bit sizes, aspect ratios, vias, challenges in drilling, and ways to enhance efficiency in the drilling department.
Elevating PCB Design Engineering With IPC Programs
04/24/2024 | Cory Blaylock, IPCIn a monumental stride for the electronics manufacturing industry, IPC has successfully championed the recognition of the PCB Design Engineer as an official occupation by the U.S. Department of Labor (DOL). This pivotal achievement not only underscores the critical role of PCB design engineers within the technology landscape, but also marks the beginning of a transformative journey toward nurturing a robust, skilled workforce ready to propel our industry into the future.